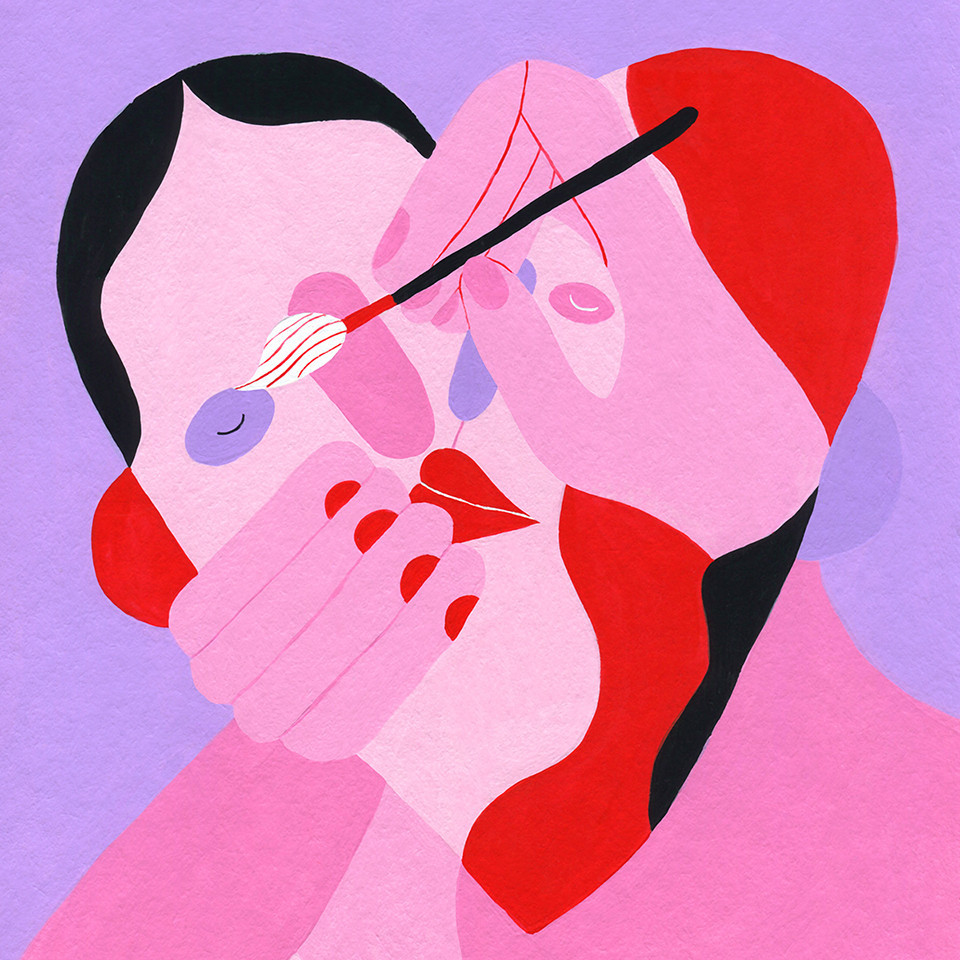
The Blue Page:
Denim news
Text by Laura Reinke
We use only the very best Italian denim – but that is really only the first step along the path to making a pair of high-quality jeans. How do we go about designing the perfect fit? From researching the latest trends to the finished product, Uwe Kippschnieder, our Denim Developer, explains everything.
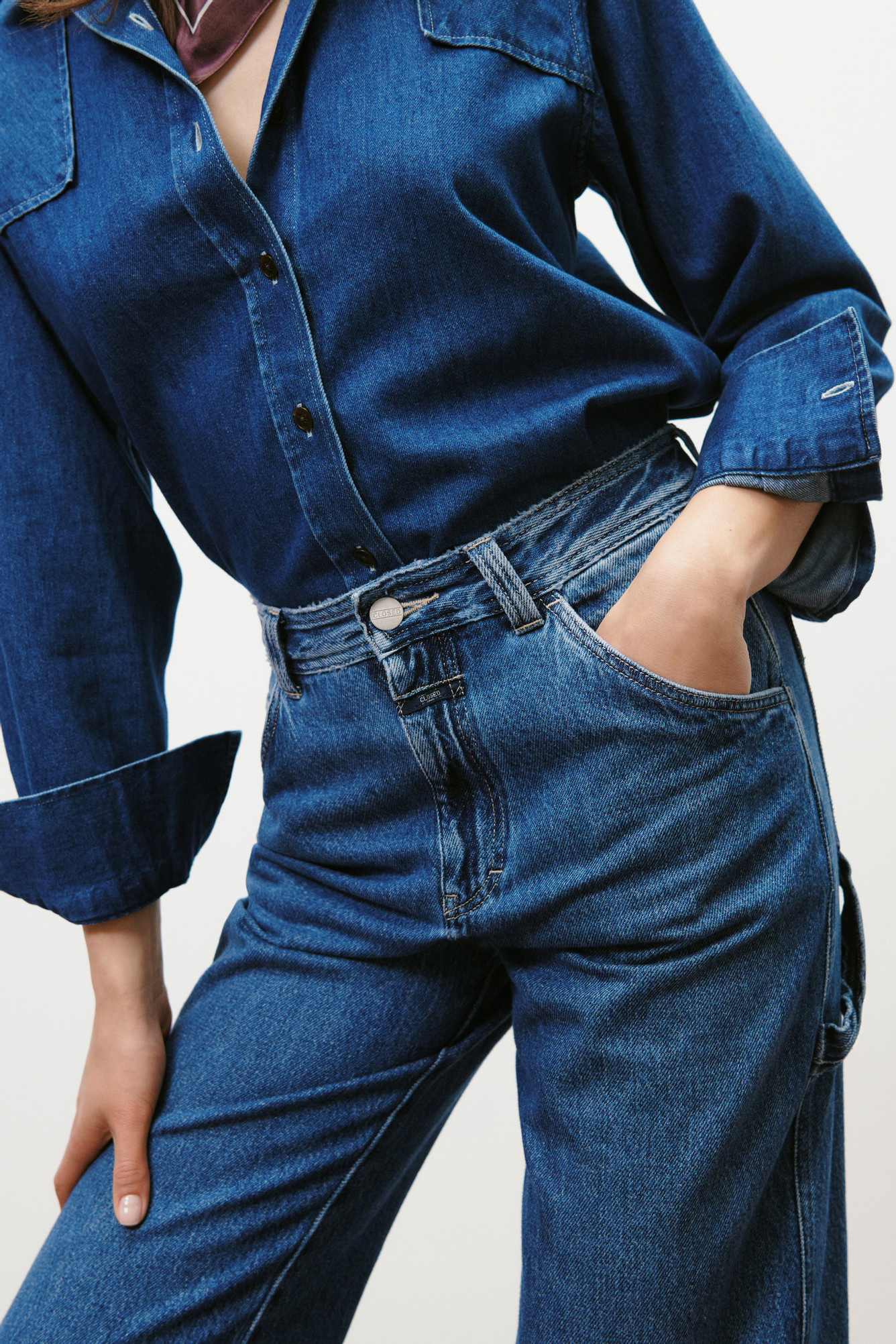
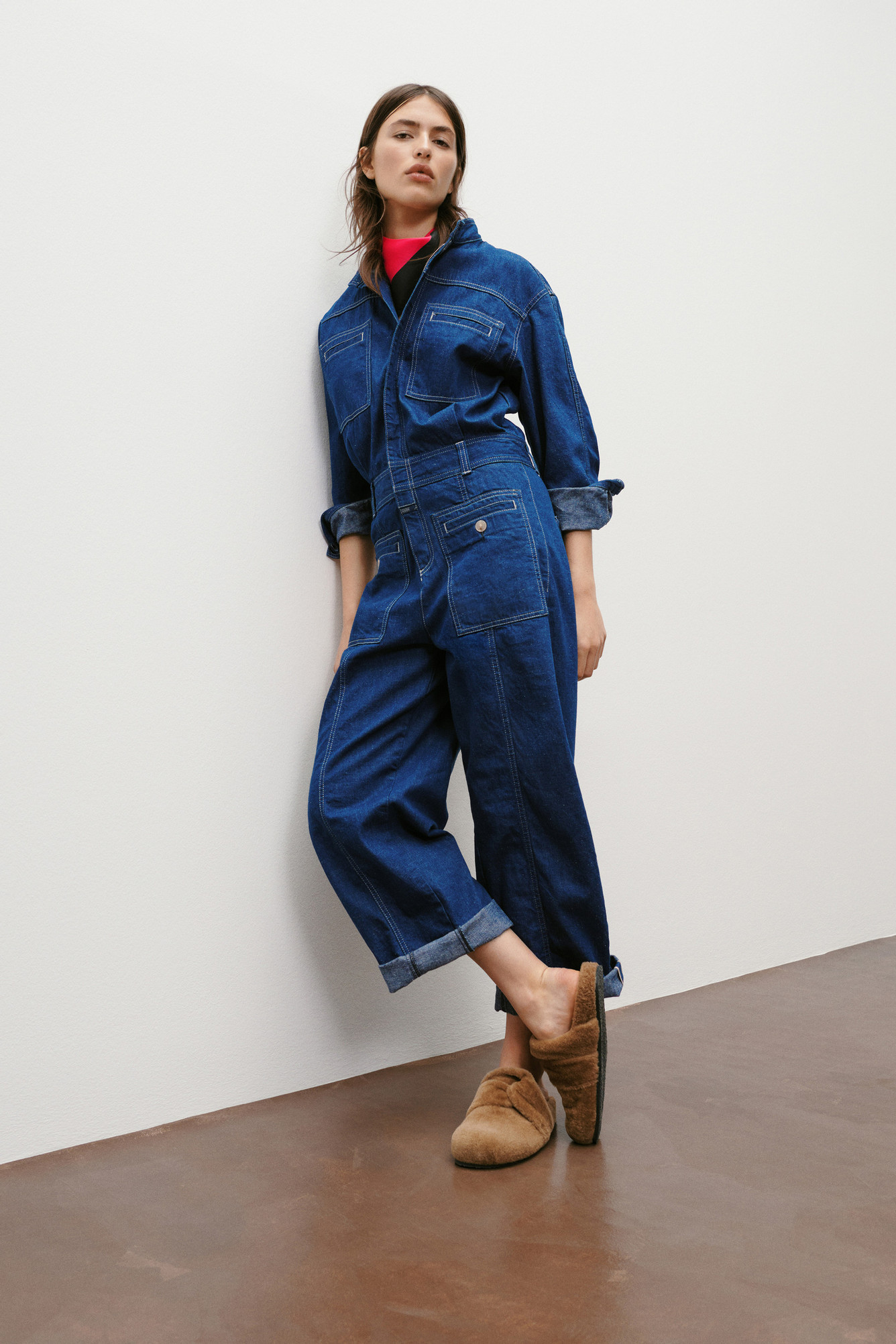
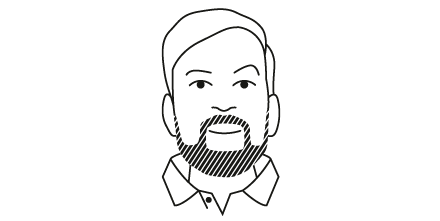
„Development can take a lot of time: as a rule it takes three to four months until we have created a new fit.“
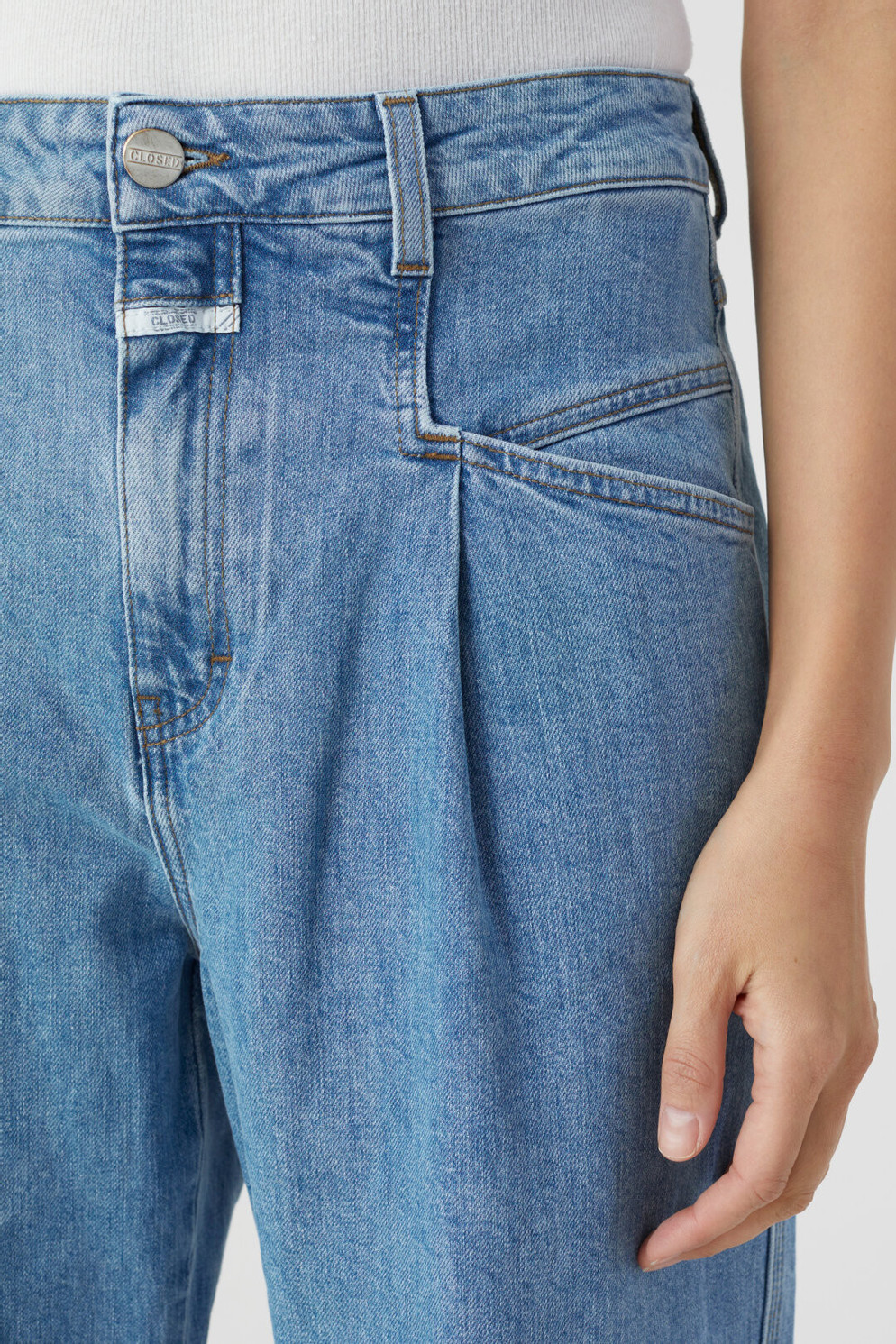
Denim Lexicon
Text by Laura Reinke
Most denim lovers appreciate it when their favourite material comes with a very minimised (but no less fascinating!) look: the selvedge denim in its pure, unwashed form. Why is it so popular and how is it different?
We asked our very own denim expert Uwe Kippschnieder.
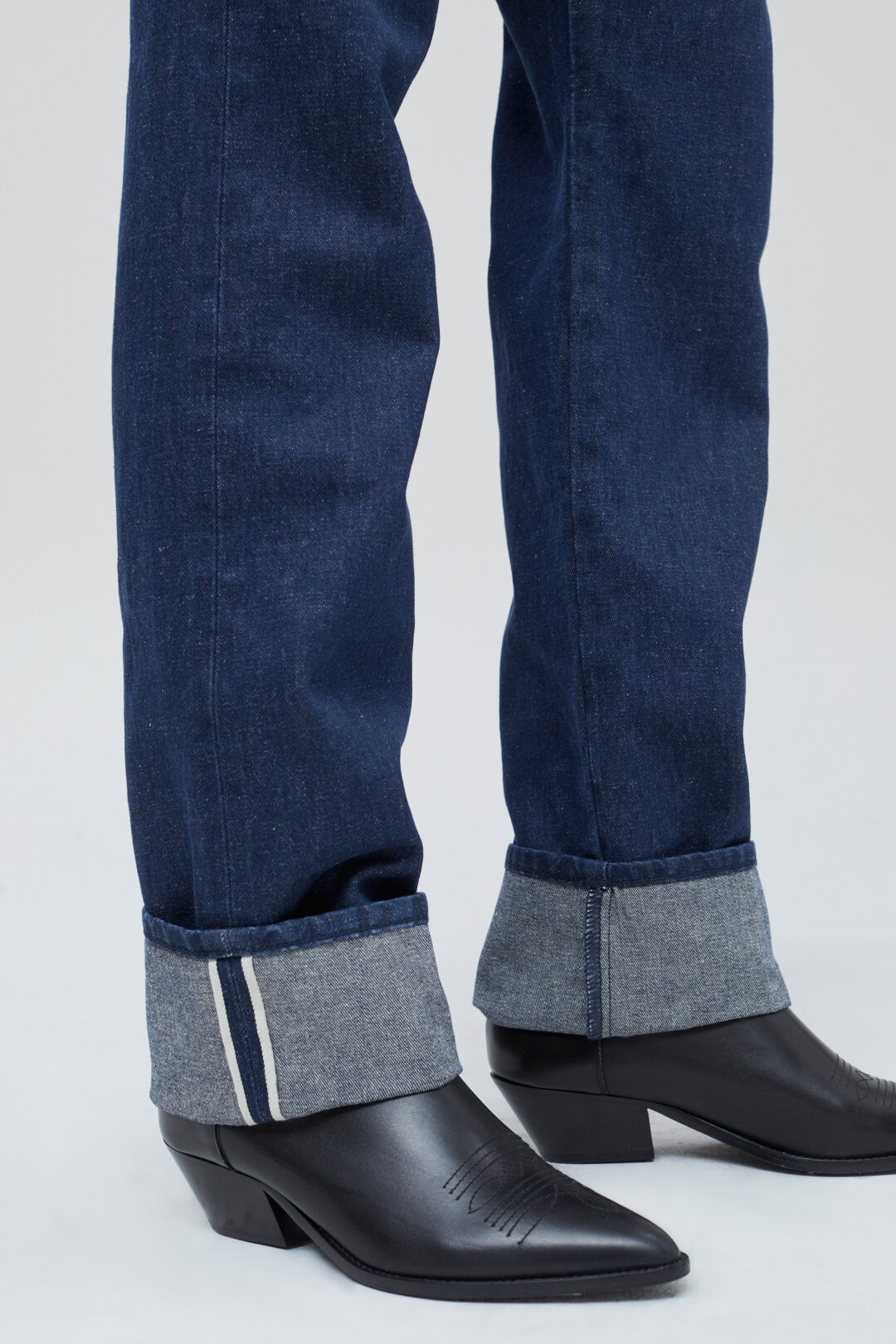
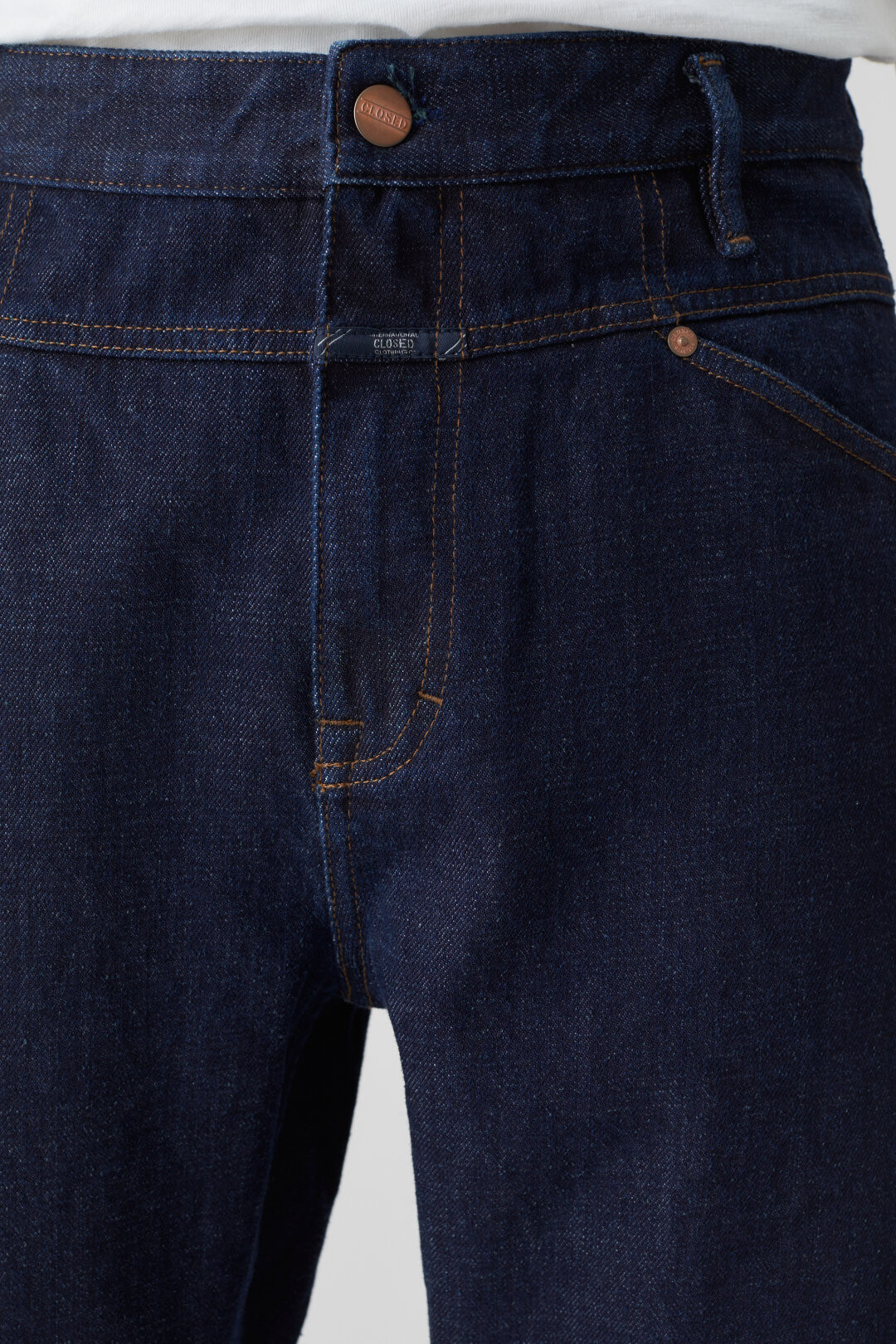
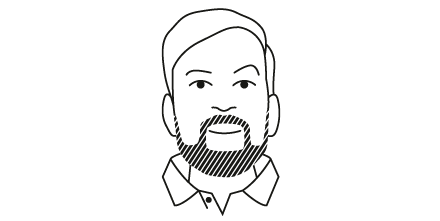
„Selvedge denim is very authentic – and among denim experts, selvedge denim is a synonym for fabrics that are of especially high quality.“
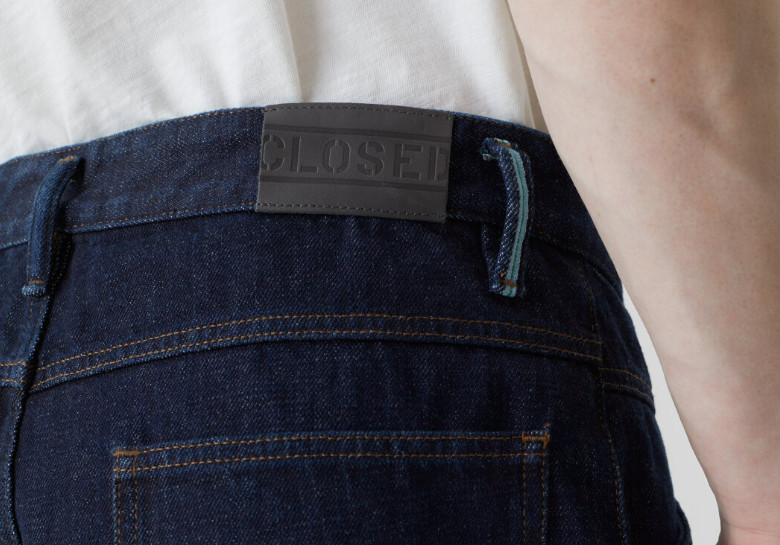
Denim Lexicon
Text by Laura Reinke
With much enthusiasm and great attention to detail, denim experts produce our jeans in Italy. They perform many of the production steps by hand, giving every pair a unique touch. In the denim world, these touches might mean destroyed details, intentional abrasions, authentic used look washes – as if the jeans had been worn for years. How is this wornout appearance achieved – and why do we love it so much?
We asked our very own denim expert Uwe Kippschnieder.
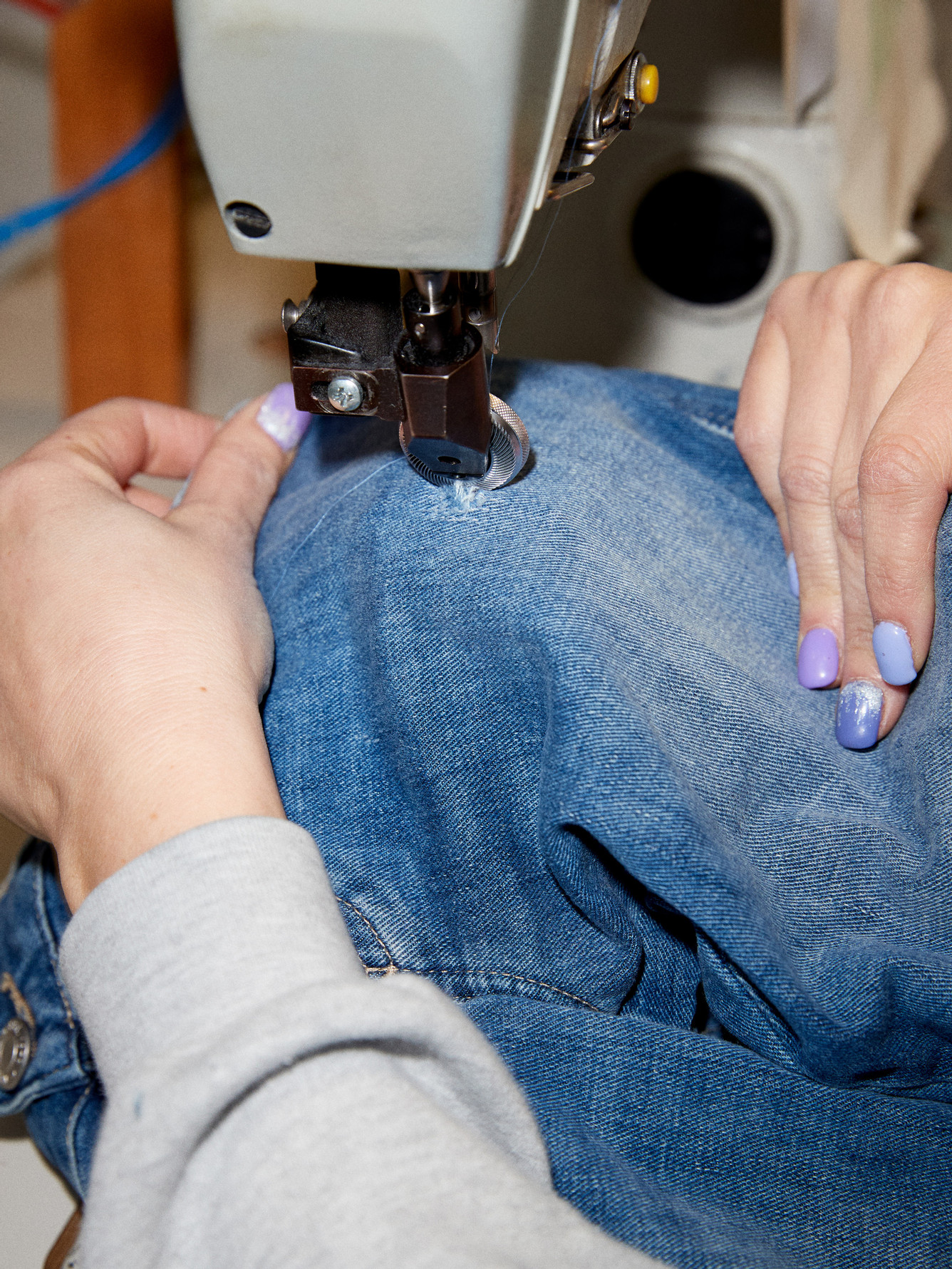
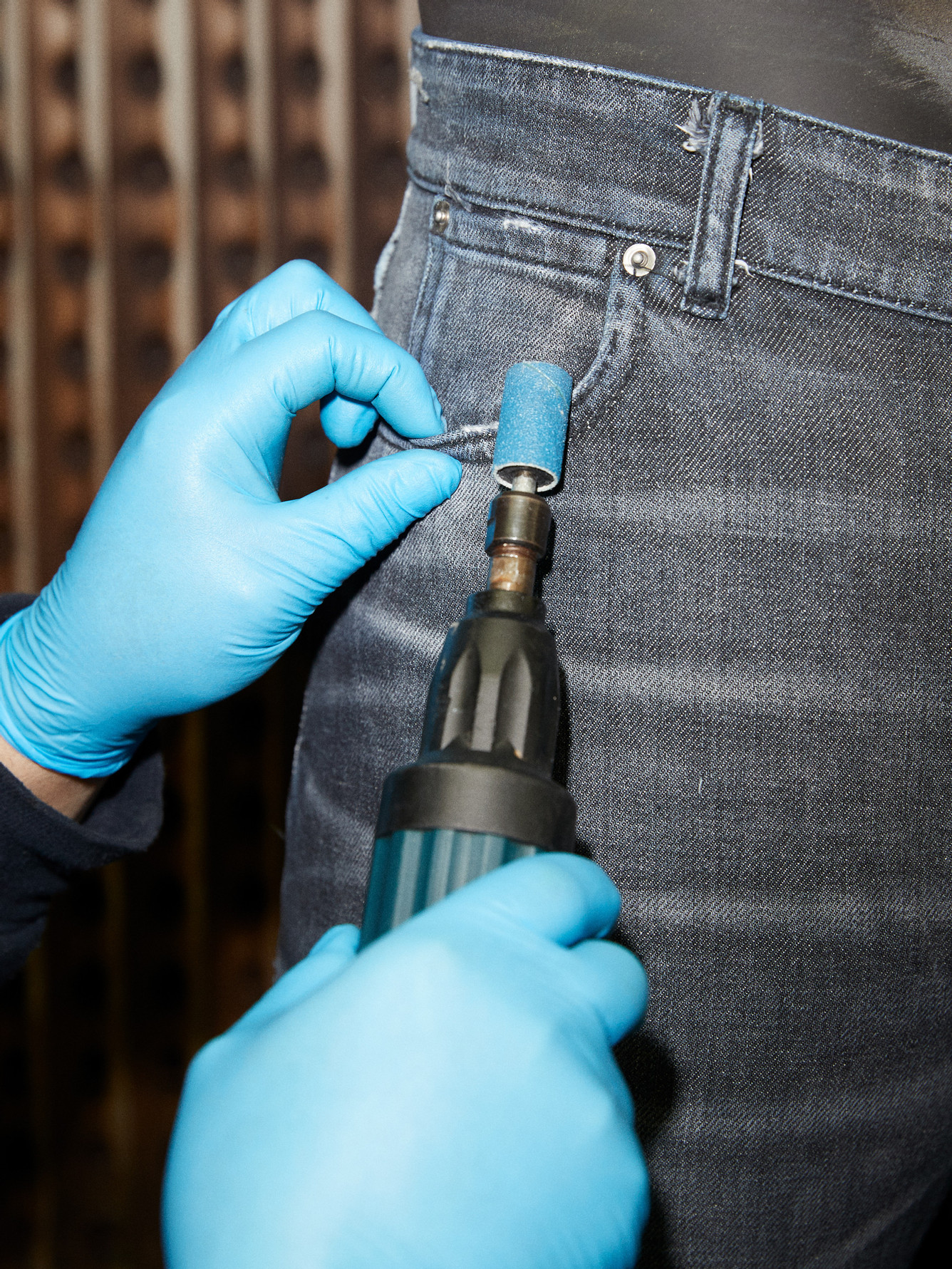
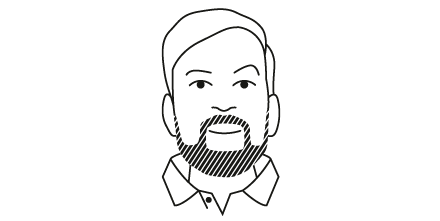
„Denim is a unique material – it becomes a favourite item that changes with time,
showing off different lighter shades of blue as the years go by.“
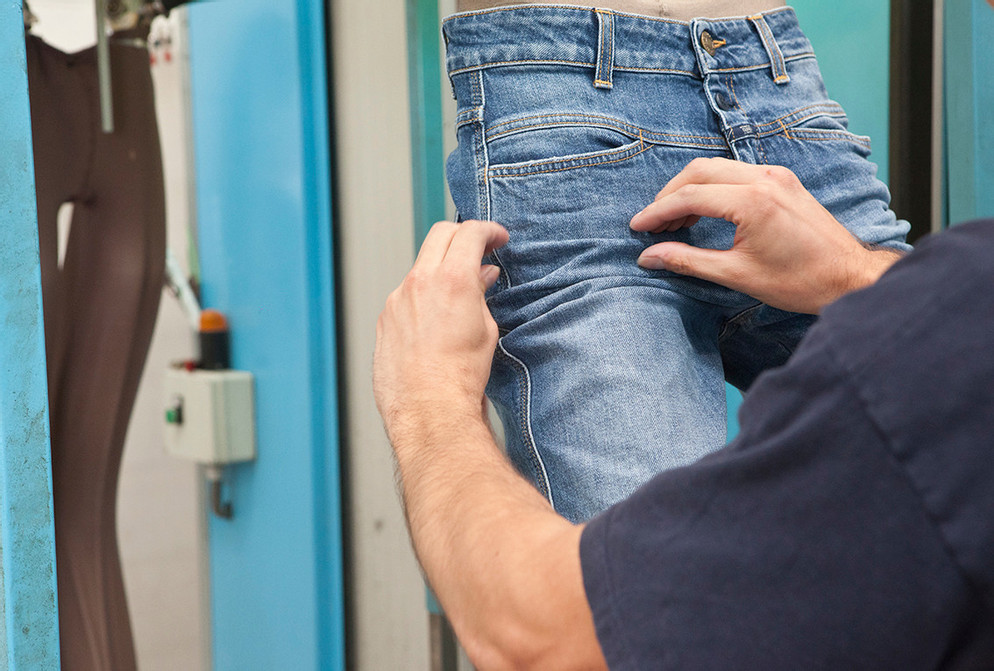
Denim Lexicon
Text by Laura Reinke
We’re always hunting for even more eco-friendly materials and techniques for our sustainable denim line A BETTER BLUE – to save even more water, electricity, chemicals and emissions. In our summer 2022 denim collection, we found two great partners that are helping us to reach this goal: linen and hemp. Linen is not only the definition of the perfect summer material thanks to its lightness, casual look and cooling properties, it also has many sustainable advantages. The same is true for hemp, another eco-friendly multi-talent. By the way, both materials are cultivated in Europe!
We asked Uwe Kippschnieder, our denim developer and sustainability expert, a few questions about linen and hemp.
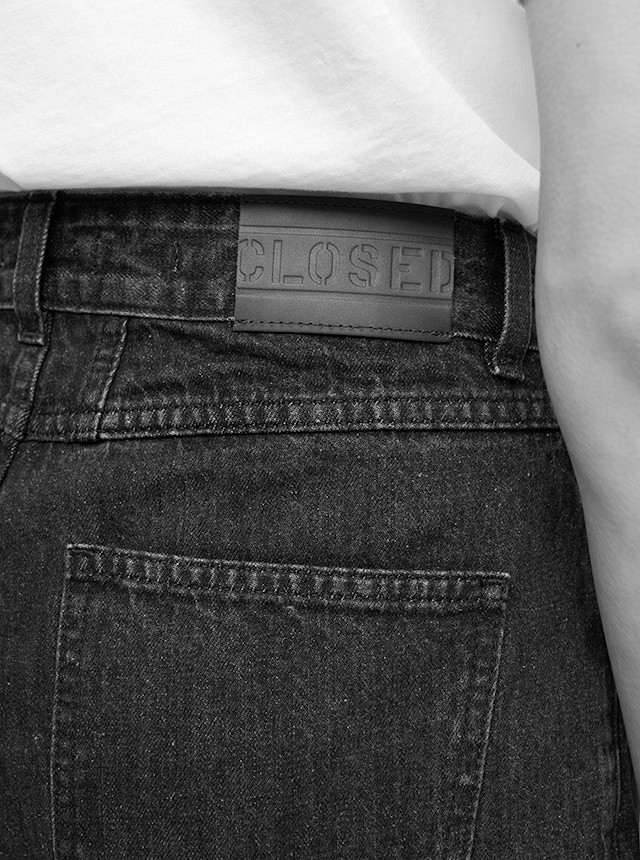
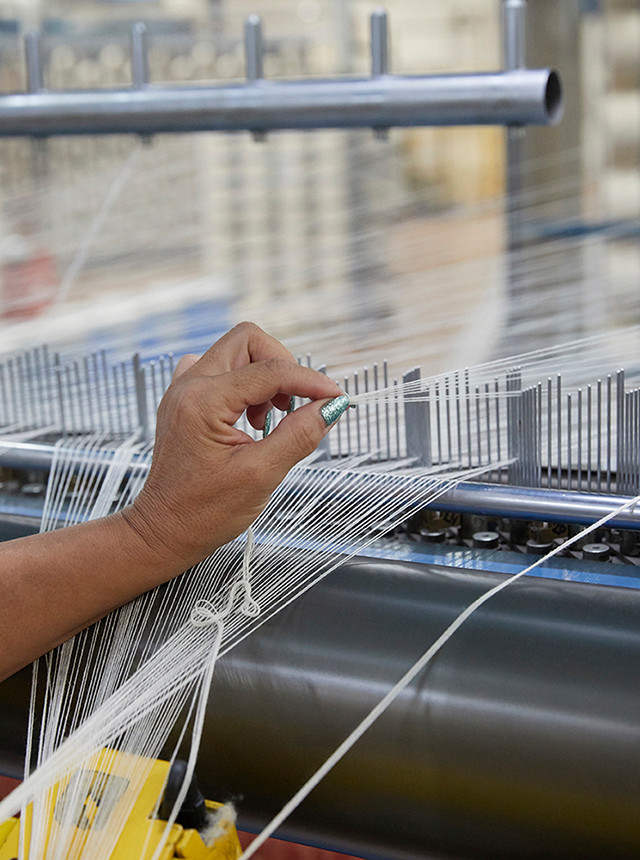
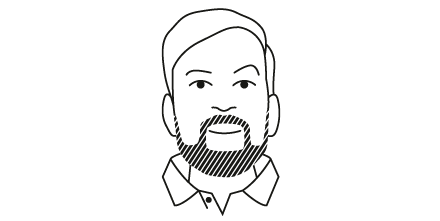
„Most of the global flax production is in Europe –for example, in France or Belgium. This results in relatively short transport routes to our fabric producers in Italy.“
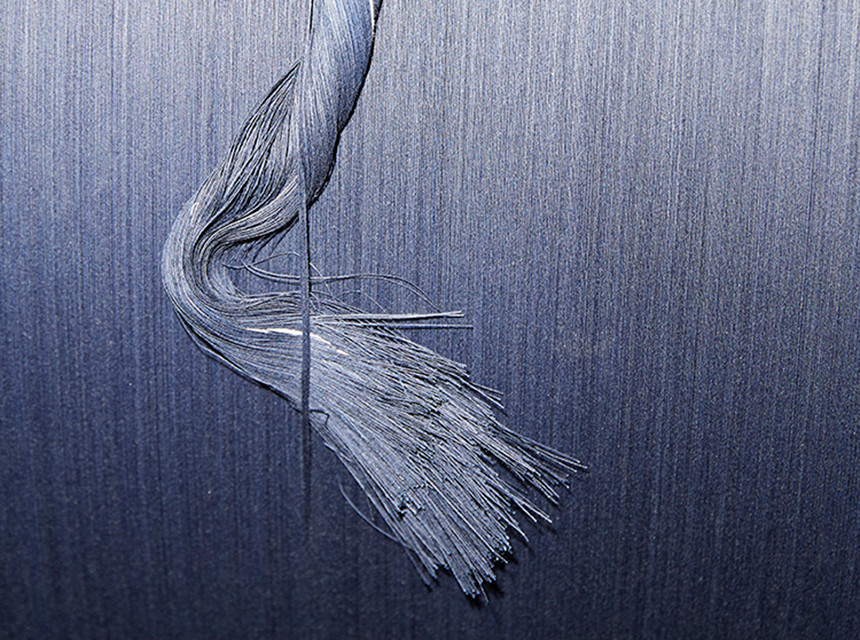
Denim Lexicon
Text by Laura Reinke
Since we started our eco-denim line A BETTER BLUE in 2018, we’re constantly on the lookout for innovative sustainable materials and techniques – to save even more water, electricity, chemicals and emissions when making our jeans. That’s why we were really excited when learning about a new low-impact way to dye our denim (and other fabrics!) with natural dyes – almost every colour is possible! We asked our very own denim developer and sustainability expert Uwe Kippschnieder a few questions about this process – and he also explains other eco-friendly dyeing methods in use for A BETTER BLUE.
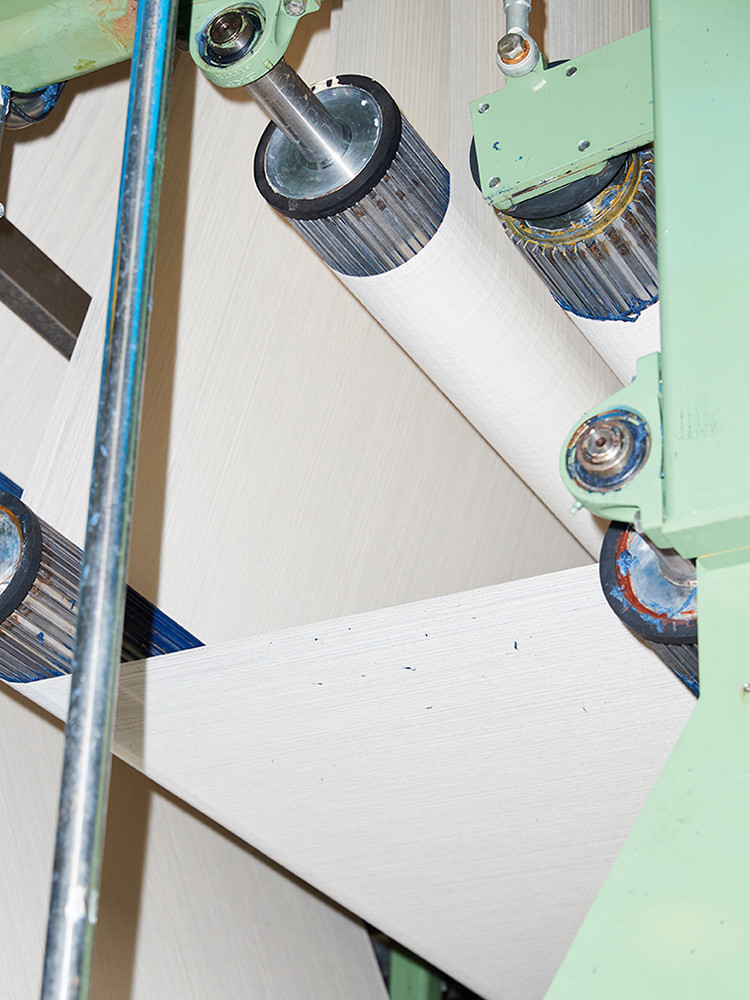
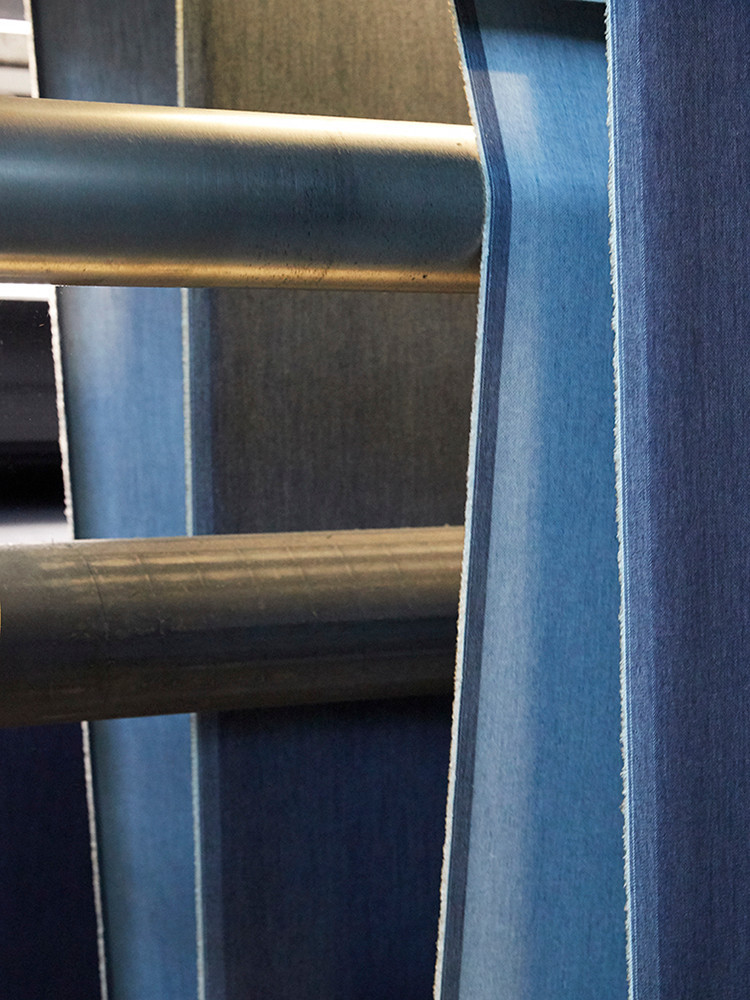
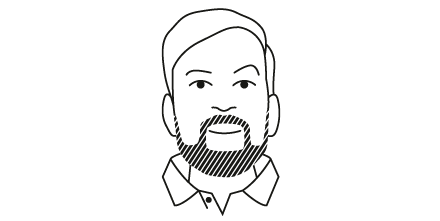
„Natural dyes are either mineral-based or plant-based.“
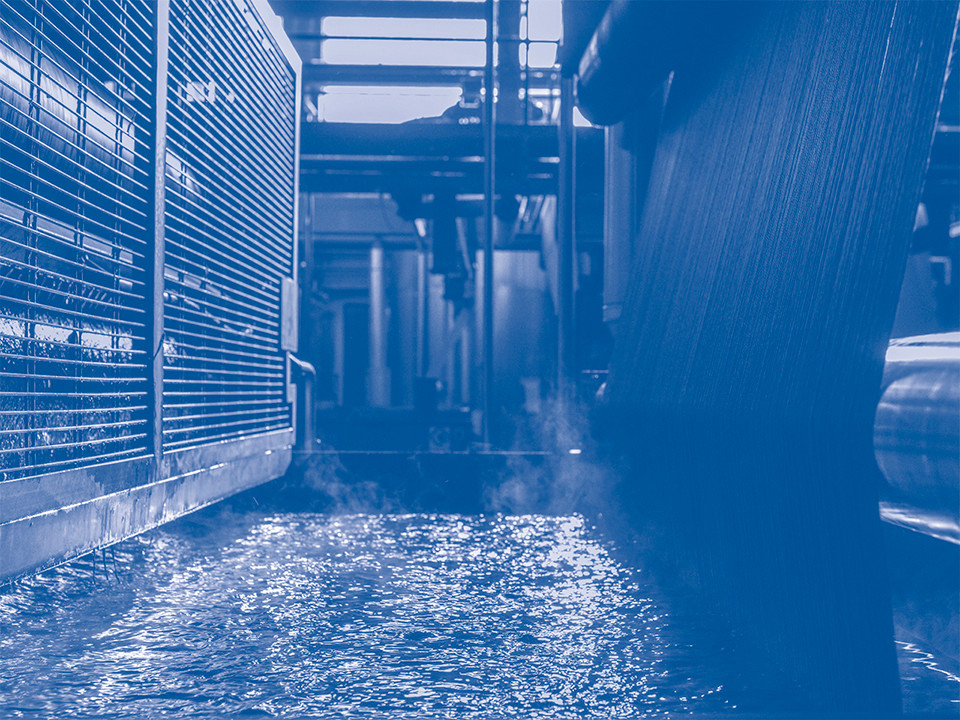
Denim Lexicon
Text by Laura Reinke
The most important ingredient of (almost) every denim: cotton! We have been switching to organic cotton for the majority of our jeans within the last years, as it’s much more eco-friendly. By now, around two-thirds of our jeans for men and women are made with organic cotton. We asked our very own denim (and cotton!) expert Uwe Kippschnieder a couple of questions about the material.
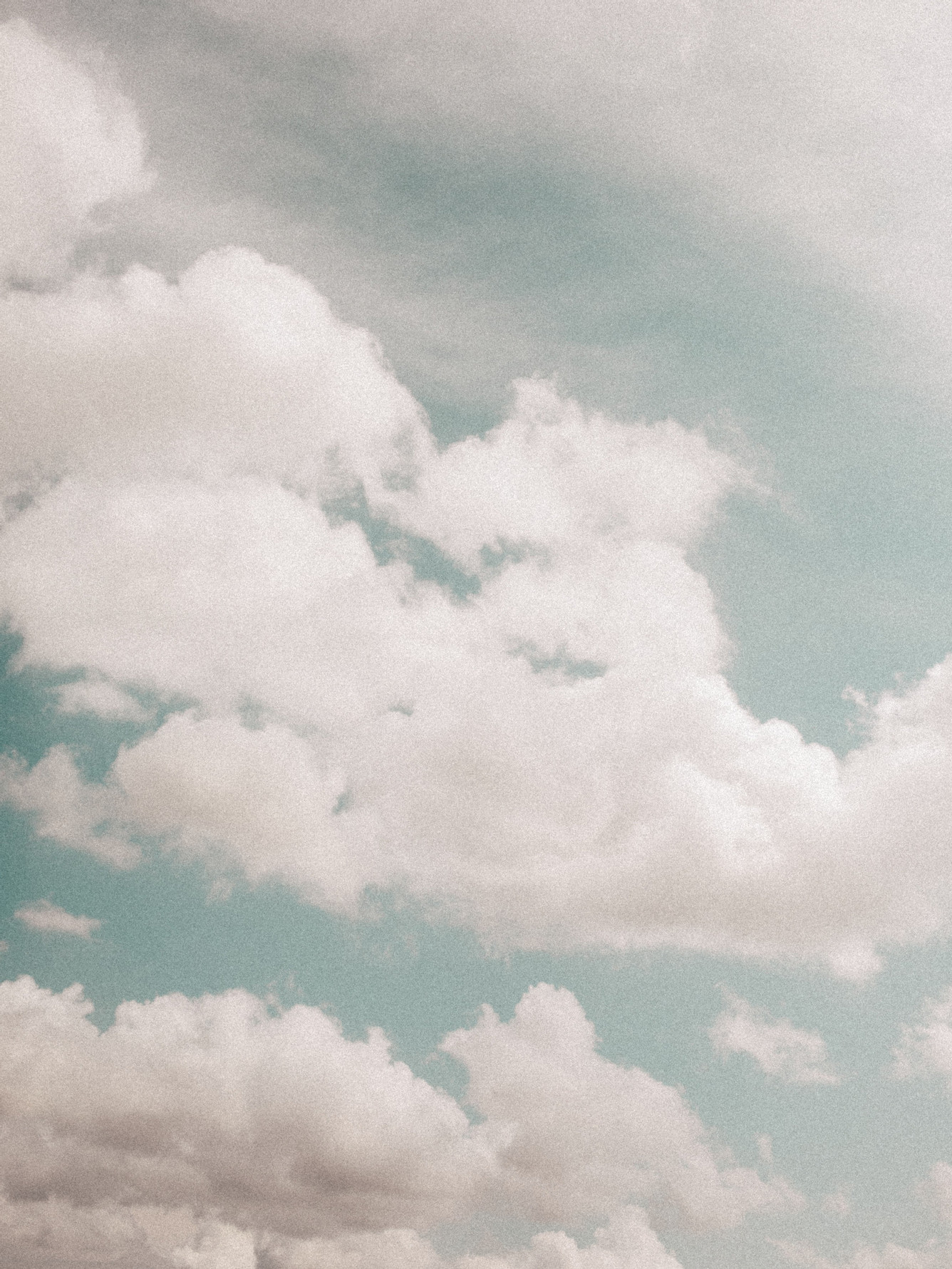
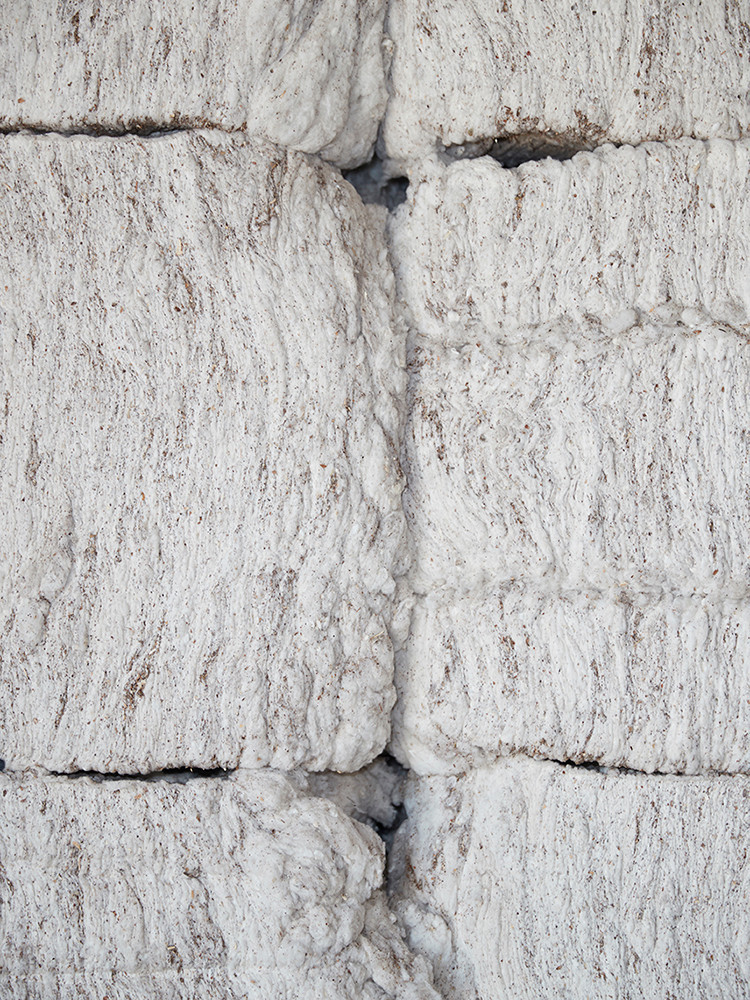
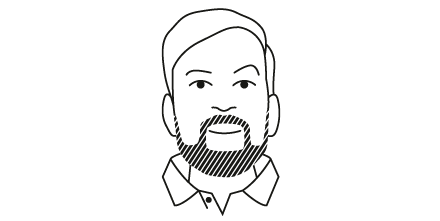
„The less virgin, conventional cotton we use, the more we can cut back on the water, energy and chemicals that would otherwise be needed to grow cotton.“
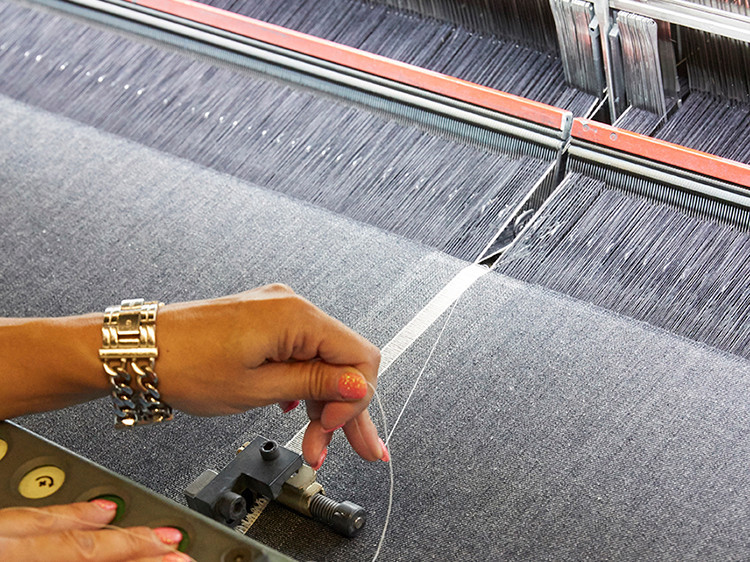
Denim Lexicon
Text by Laura Reinke
Our denim wouldn’t have its signature blue hues – from spring sky to dark navy – without elaborate wash treatments. Our denim laundries in Italy, Everest and Green Lab, focus on state-of-the-art sustainable techniques to save water, chemicals and energy – while creating every conceivable shade of blue. We talked to our denim expert Uwe Kippschnieder about the latest eco-friendly wash innovations.
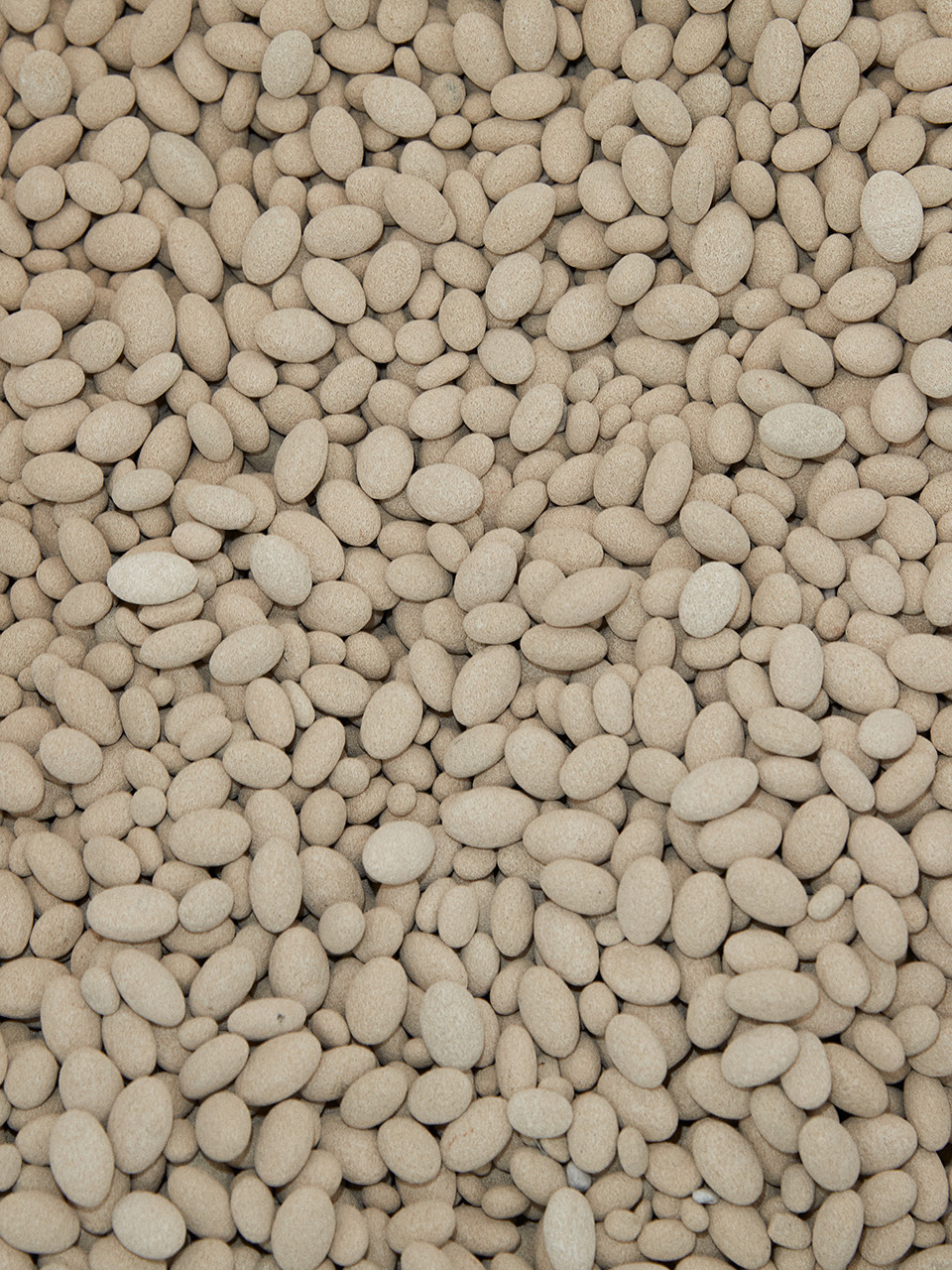
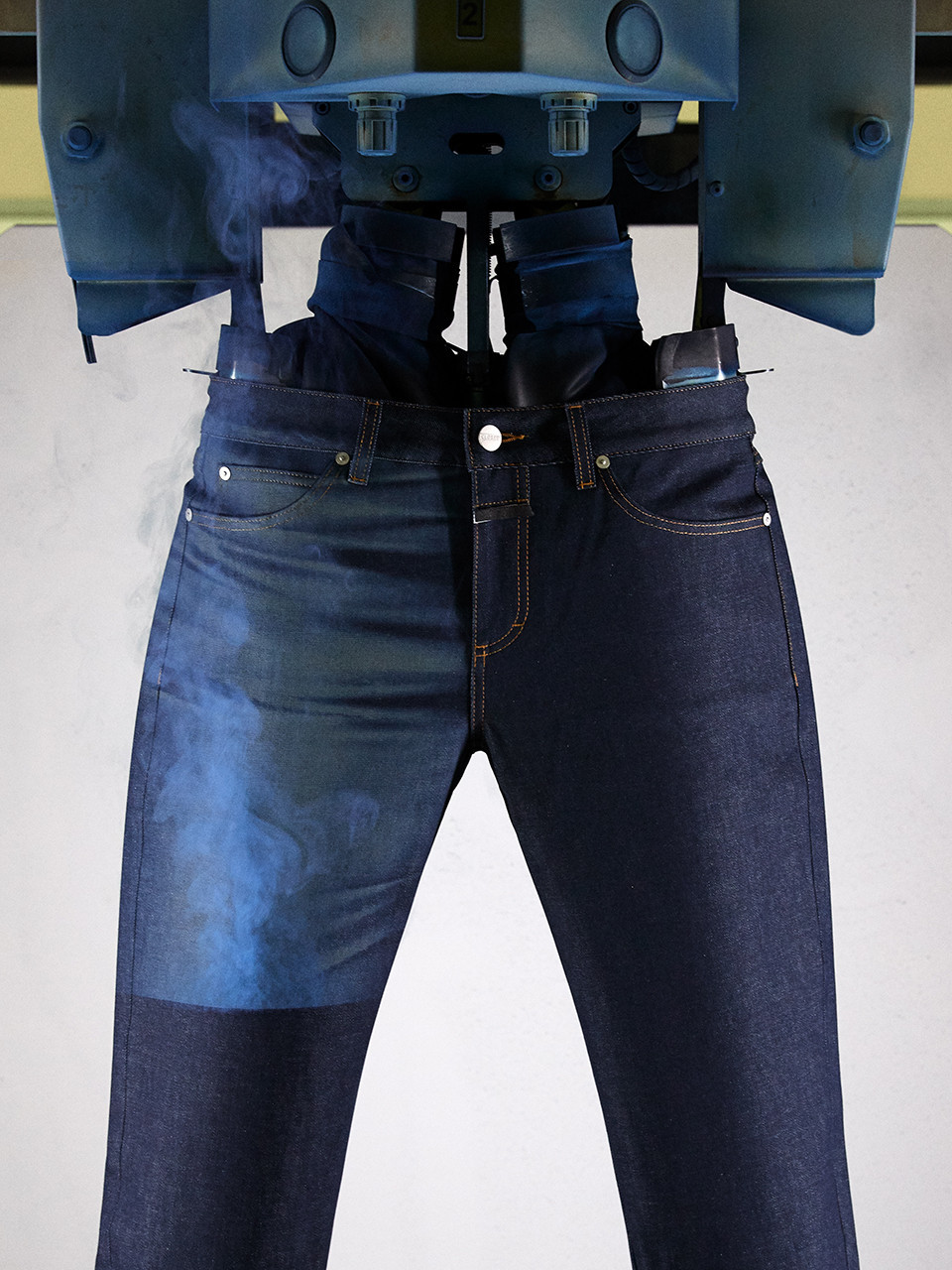
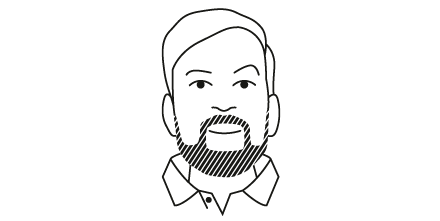
„We also wash with ozone, a naturally occurring gas.“
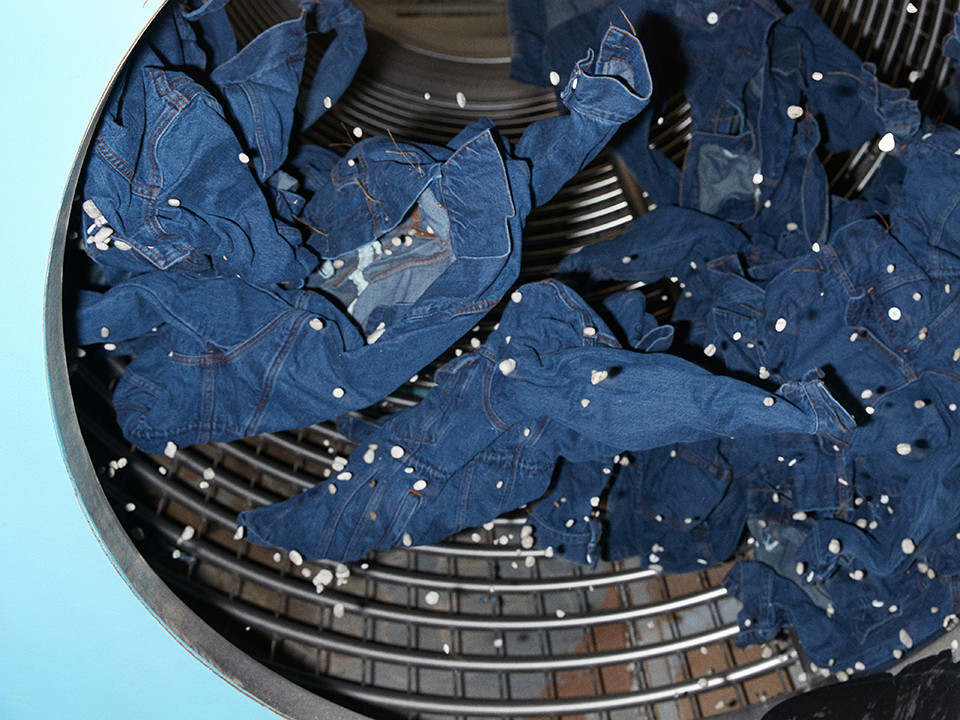
Denim Lexicon
Text by Laura Reinke
For our eco-denim line, A BETTER BLUE, we’re always looking for innovative sustainable materials and techniques – to save even more water, electricity, chemicals and emissions when creating our jeans (all of them are 100% Italian-made, by the way). As it’s much more efficient to use existing resources to create something new, we have been using recycled materials for our denim for a while now – and we’re excited to be introducing jeans with PCR cotton (post-consumer recycling cotton) content very soon! PCR cotton is made of cotton garments that have reached the end of their lifespan. By using old clothes to make new ones, precious resources are saved – allowing us to move towards a circular economy. For these reasons, our Italian denim mill Candiani has started a PCR program with several local partners, aimed at reviving discarded clothes to give them a second life. We asked our denim developer and sustainability expert Uwe Kippschnieder a few questions about this eco-friendly novelty.
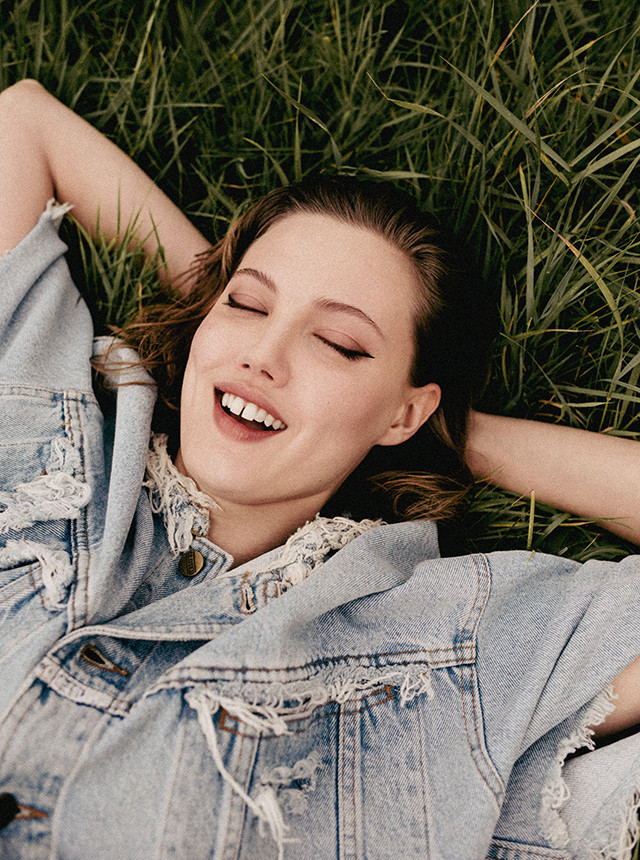
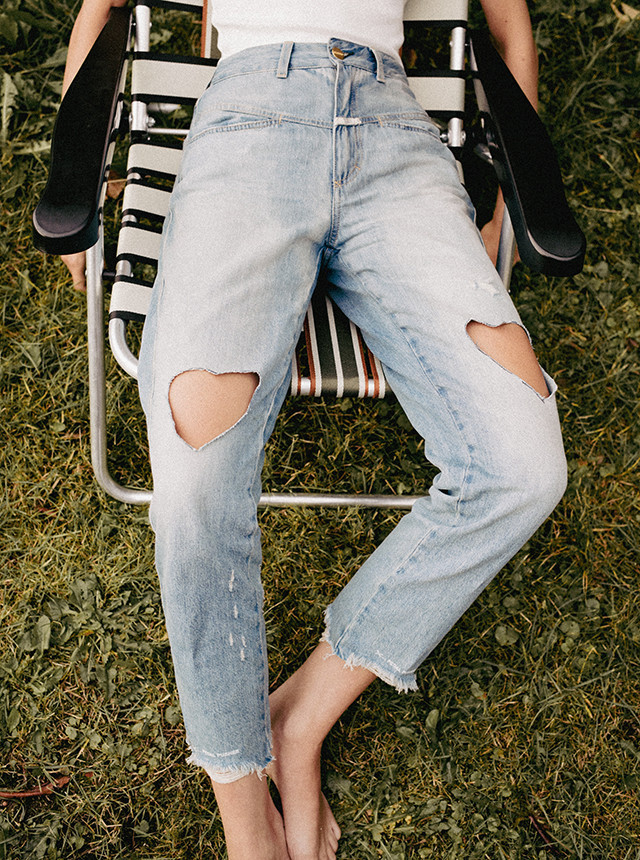
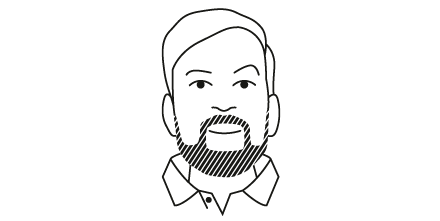
„We can decrease garment waste and fewer resources are necessary to produce new materials.“
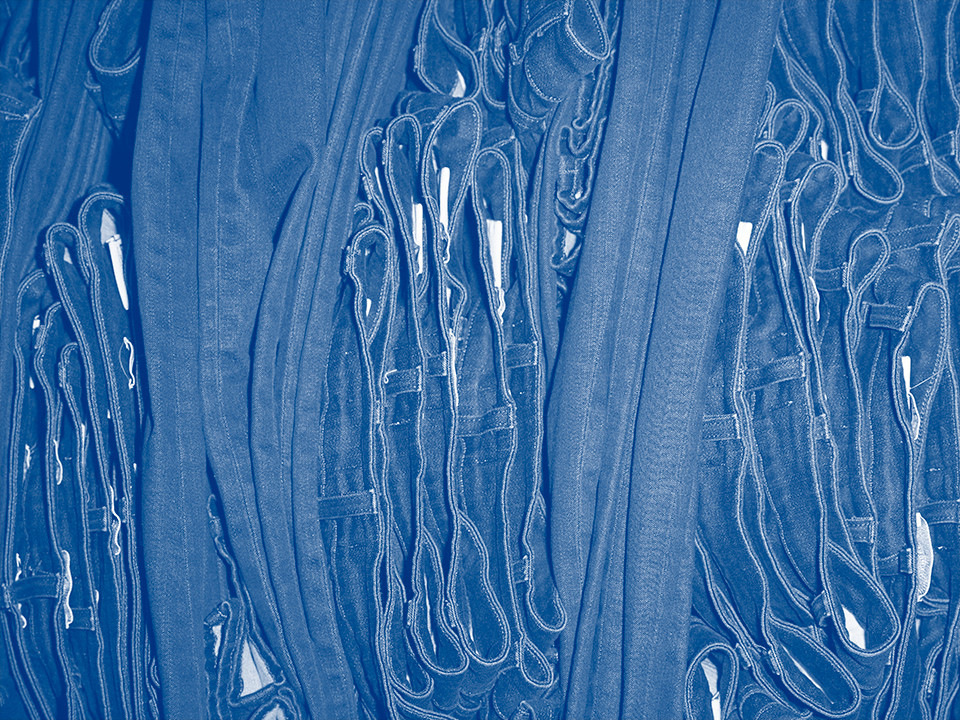
Denim Lexicon
Past Stories
Copy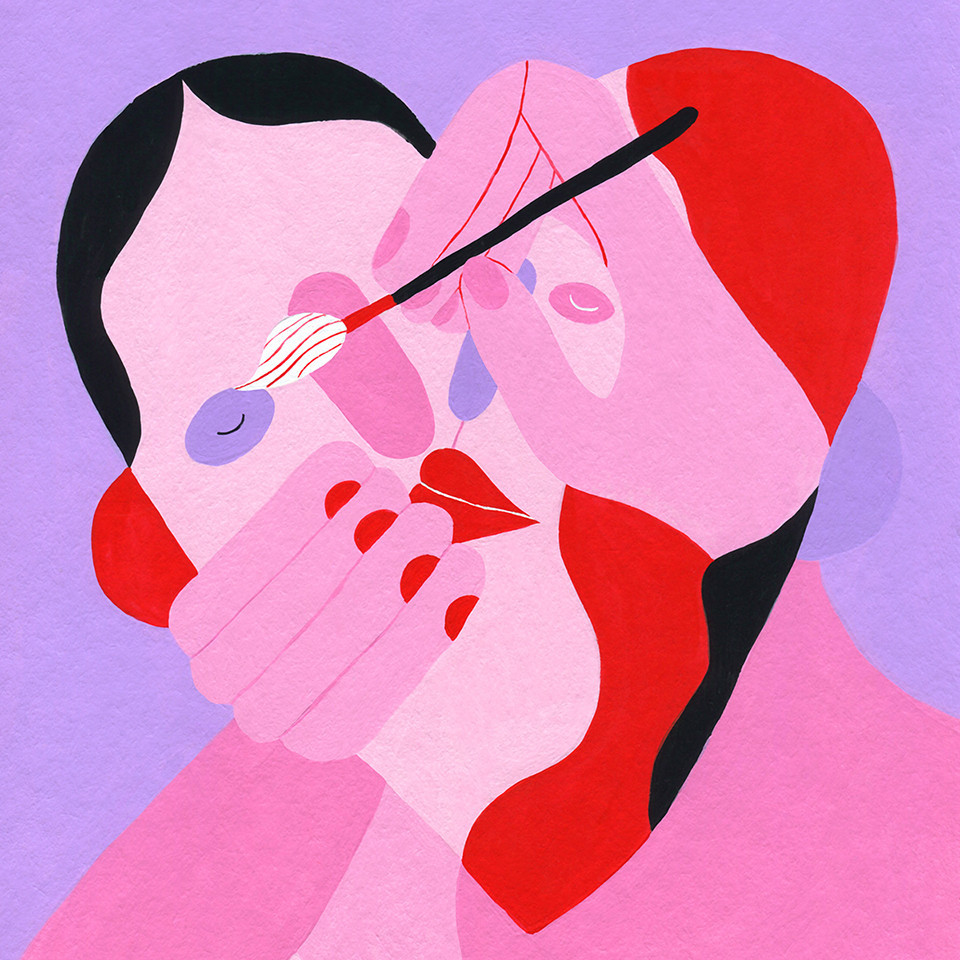